Table of Contents
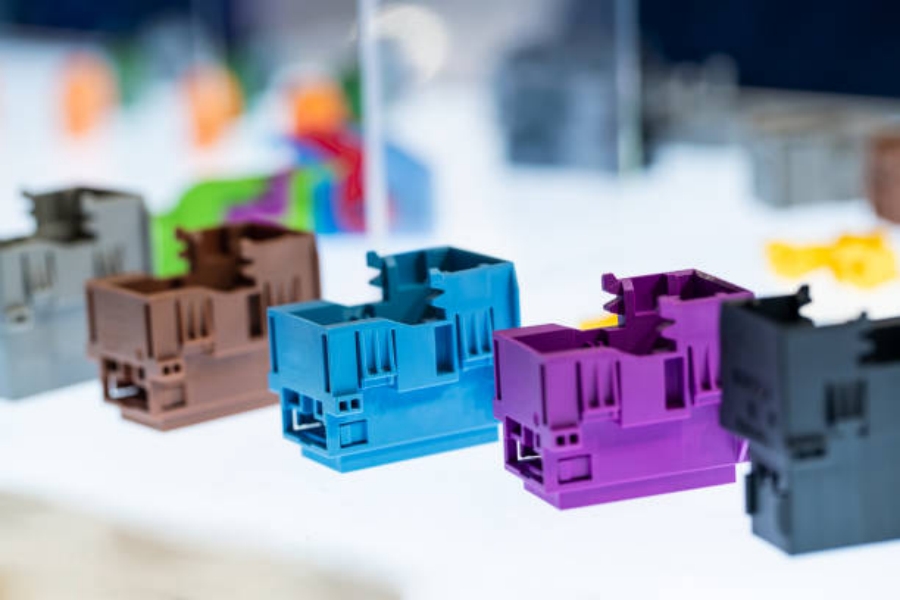
Introduction
If you work with any kind of equipment that involves fluid flow, chances are you're familiar with electrical pressure switches. These switches monitor the pressure of fluids passing through pipes, and they can activate alarms, pumps, valves, or other devices to maintain safe and efficient fluid flow. In this guide, we'll explore the key features of electrical pressure switches and how they work, as well as their applications, benefits, and maintenance requirements.
What is an Electrical Pressure Switch?
Simply put, an electrical pressure switch is a device that measures the pressure of a fluid system and controls its electrical output accordingly. It consists of a pressure-sensitive spring mechanism, a set of electrical contacts, and a mechanical actuator such as a piston or diaphragm. When the pressure in the system reaches a pre-set level, the actuator triggers the electrical contacts, which can then activate or deactivate other equipment.
How Does an Electrical Pressure Switch Work?
When a fluid flows through a pipe, it exerts a pressure that can be measured by a gauge or a transducer. The pressure switch is connected to this gauge, and it is set to a specific pressure range by adjusting the spring tension or a screw. When the pressure goes beyond or below this range, the switch actuates and performs the designed function, such as turning on a pump or shutting off a valve. Some pressure switches have adjustable hysteresis, which means they can switch on and off at different pressure levels to avoid rapid cycling or erratic behavior.
Applications of Electrical Pressure Switches
Electrical pressure switches are used in a wide variety of industrial and commercial settings, including water treatment, HVAC, oil and gas, food and beverage, pulp and paper, medical, and transportation. Some common applications include:
- Controlling the water level in a tank or reservoir
- Protecting a pump from low pressure or dry running
- Regulating the pressure in a compressed air system
- Stopping a conveyor belt if the material flow is interrupted
- Preventing an HVAC system from over- or under-heating
- Detecting leaks in pipelines or vessels
Benefits of Electrical Pressure Switches
Using an electrical pressure switch in your fluid system can offer several advantages:
- Efficient and reliable monitoring of fluid pressure
- Easy integration with automation systems and control panels
- Customizable pressure settings and output configurations
- Low maintenance requirements and long service life
- Cost-effective alternatives to more complex sensing devices
Types of Electrical Pressure Switches
There are several types of electrical pressure switches that differ in their design, construction, and performance characteristics.
- Mechanical pressure switches - the most basic type that use a spring or a piston to activate the contacts.
- Diaphragm pressure switches - employ a flexible diaphragm that bends in response to pressure changes, suitable for higher accuracy and precision.
- Differential pressure switches - compare the pressure between two fluids or systems and trigger the contacts if the difference exceeds a set threshold.
- Vacuum pressure switches - designed to detect low-pressure conditions or vacuum levels.
- Electronic pressure switches - use advanced sensors and microprocessors to measure pressure and provide additional features such as LED displays, digital readouts, and wireless communication.
Factors to Consider When Choosing an Electrical Pressure Switch
When selecting an electrical pressure switch for your application, you should take into account several factors:
- The pressure range and accuracy requirements of your fluid system
- The electrical load and rating of the switch
- The environmental conditions such as temperature, humidity, and vibration
- The material compatibility with the fluid and the system components
- The installation and mounting requirements
Installation and Maintenance of Electrical Pressure Switches
To ensure the proper functioning and safety of electrical pressure switches, you should follow these guidelines:
- Read and understand the manufacturer's instructions and specifications
- Install the switch in a suitable location and orientation that allows access and visibility
- Use proper wiring and grounding techniques, and protect the switch from overvoltage or short circuits
- Calibrate and test the switch periodically, and replace it if it shows signs of wear or damage
- Inspect the system and the fluid regularly for leaks, corrosion, or contamination that can affect the switch performance
Conclusion
Electrical pressure switches are essential components in fluid systems that require precise and reliable pressure monitoring and control. They offer a versatile and cost-effective solution that can help optimize your processes and prevent costly errors and failures. By understanding the basic principles, types, applications, and maintenance requirements of electrical pressure switches, you can make informed decisions and ensure the safety and efficiency of your fluid handling systems.